Metal Stitching & Crack Repair of Cast Iron Flood Control Pump Element for the City of Sacramento
Step by Step Report Presentation (PDF - 1.59 MB)
We were recently contracted by The City of Sacramento to repair a crack in the corner of the port/flange area of a 5 million gallons per day flood control pump. At LOCK-N-STITCH Inc. we specialize in metal stitching technologies and machining, which are both processes that were necessary to provide the cost effective solution they needed.
The pump discharge port flange area cracked during replacement of the gate valve. In that repair the raised hub of the gasket surface of the new gate valve placed excess pressure on the flange and caused the crack. (Raised hub flanges should never be bolted to a cast iron flat faced flange.)
The contractor had never even heard of metal stitching so he consulted with the welding rod suppliers, manufacturers and even the American Welding Society for a procedure to weld the casting. They attempted to arc-weld the crack with 99% nickel rod. Prior to this welding they had Vee’d out the cracks from both sides. The problem with welding cast iron is that once it’s done it cannot be machined, thereby ruling out metal stitching. If used initially, metal stitching could have solved the problem.
Primary steps involved remediation work to remove nickel rod that had been arc welded in a previous attempt to seal the cracked section. To properly repair the damaged area we were forced to replace the 2" thick, 5’ diameter flange. To remove the flange, a portable mill was set up and dialed-in to the face and then removed using an abrasive cut-off saw. The end of the discharge port was then hand ground to remove the hardened iron from the previous welding and machined flat and parallel to the original flange face. By completing this initial process the cast iron was prepped now to accept our metal stitching application. Six equally spaced 3" x 4" slots were machined into the end of the port, which were designed to accept steel locking-lugs that had been welded in to the newly fabricated steel flange. We then used our patented Castmaster® C3D stitching pins around the entire repair, including the locking-lugs for added joint strength.
We then use an overlapping process to assure that no gaps were left between our stitching pins which ensure a pressure tight joint. After the stitching process we conducted magnetic particle inspections, and pressure testing to 80 psi.
The entire project was completed in just 3 weeks, and was quite a unique project as it was a second attempt solution for the 1919 manufactured pump. Without the option of replacement parts a new pump would have cost the City of Sacramento over 1 million dollars. Our innovative cast iron repair cost the city only $80,000, a huge cost savings to their budget.
To learn more about this project, or the processes used to repair it, see the table below or contact us directly.
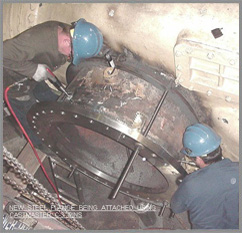
to the pump casting

to arc weld on it
Highlights of the Metal Stitching & Crack Repair Project
- Cast Iron Crack Repair Capabilities Applied/Processes
- Primary: Metal Stitching
Secondary: In-house and on-site machining, fabrication
- Equipment Used to Manufacture Part
- Portable Mill, abrasive cut-off saw, locking-lugs, C3D CASTMASTER Stitching Pins
- Overall Part Dimensions
- 5ft diameter discharge. The casting wall is 2" thick .
- Material Used
- Iron
- In process testing/inspection performed
- Magnetic particle inspection, pressure tested to 80 psi
- Industry for Use
- Pumps
- Volume
- 5 million gallons a day
- Delivery/Turnaround Time
- November, 2000. Three weeks repair time.
- Delivery Location
- Sacramento City
- Standards Met
- Customer Specifications
- Additional Facts
- The pump was manufactured in 1919 and the damaged half could not be replaced.
A new pump would cost over 1 million dollars to install.
The total repair price was $80,000.00.
More Engine Metal Stitching & Crack Repairs
Chevron P6 Pump Final Report (PDF - 9.68 MB)