We are relocating our LOCK-N-STITCH Inc. production facility in Turlock, California, closer to other Wärtsilä locations, as part of our efforts to streamline operations.
Here’s what this means for you:Orders from current stock - We will continue to fulfil orders for items currently in inventory
Complete repair solutions - We will focus on complete repair solutions which means that some products will be unavailable in the future; we might consider providing certain single components upon separate agreement and availability
We expect this transition to continue through the end of the year. If you have questions or need help finding alternatives, we’re here to support you.
Need support? Visit us: wartsila.com
Repair Services
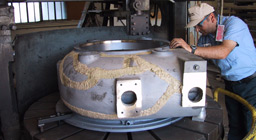
- Metal Stitching
- In-house and On-site Machining Services
- Inspection & Testing Services In-shop or On-site
- Precision Thread Repair Services


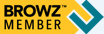
& Portfolio
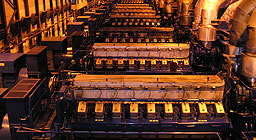
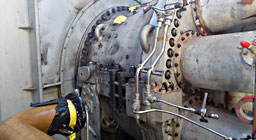
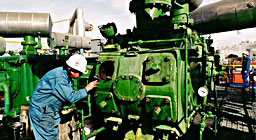
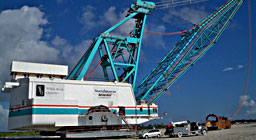
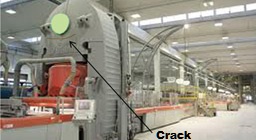
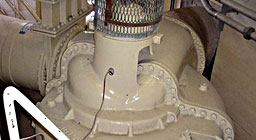
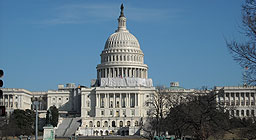
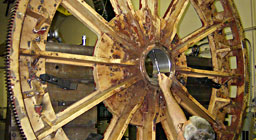
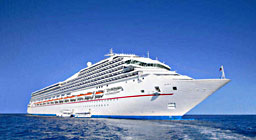
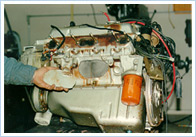
Cast iron only cracks when it is stressed beyond its tensile strength. This includes all heat related cracks, freeze cracks, impact and bending loads. Cast iron does not weaken over time. It does change if exposed to high temperatures over long periods of time like exaust manifolds and wood burning stoves. The process is called graphitization. The carbon is changed to graphite and any type of welding that requires melting the cast iron becomes very dificult because the filler metal will not bond properly. Brazing is not affected because the iron is not melted during the process. Click here to learn more